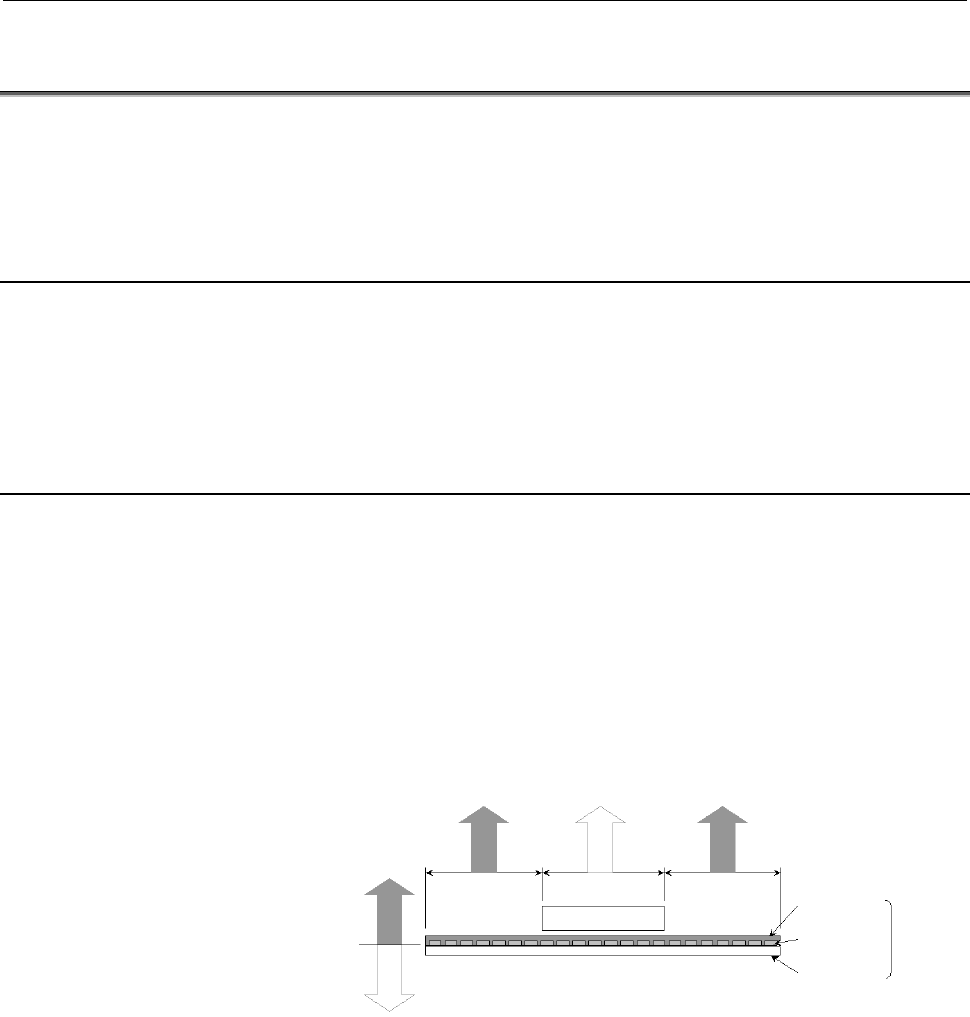
B-65382EN/02 HANDLING, DESIGN, AND ASSEMBLY 2.MECHANICAL DESIGN
- 161 -
2.18 MAGNETIC LEAKAGE AND MAGNETIC SHIELDING
Powerful permanent magnets are used for a magnet plate, so that a
magnetic material, if any near the magnet plate, can be magnetized.
This section describes the method of shielding magnetic leakage from
a magnet plate.
2.18.1 Level of Geomagnetism
According to a publication such as a chronological table of science,
the geomagnetism is 1 to 6 mT. On the other hand, the FANUC
laboratory finds that a geomagnetism of about 20 mT is observed at a
location far from a magnet plate. The level of 20 mT is found in the
routine life environment and poses no problem.
2.18.2 Magnetic Leakage
A magnet plate manufactured by FANUC consists of a base iron plate
on which permanent magnets are attached. The base iron plate is
sufficiently thick to allow little downward magnetic leakage from the
magnet plate. On the magnet side, there is little magnetic leakage in
the area that faces the coil slider. Magnetic leakage occurs in other
areas where the magnet plate is exposed. Even in this case, the level of
magnetic leakage is as low as the level found in the daily life
environment at a location 20 cm or more away upward or sideward
from the magnet plate. There is little magnetic leakage downward
from the magnet plate.
Magnet plate
Magnetic
leakage
Magnetic
leakage
Magnetic
leakage
Magnetic
leakage to 0
Magnetic
leakage to 0
Coil slider
Iron plate
Magnet
Resin